Five Easy-To-Avoid Mistakes When Installing CPVC Pipe
-
CPVC pipe problems can arise from installation errors, incompatible materials, and improper handling, but correct practices can mitigate these issues.
-
Proper thermal management, the use of compatible materials, and precise solvent application are key to maximising CPVC pipe system longevity.
-
Training and resources are crucial for ensuring that installations meet industry standards and prevent future plumbing failures.
Here are several factors contributing to early failures of FlowGuard Chlorinated Polyvinyl Chloride (CPVC) pipes and fittings, and how to address these CPVC pipe problems effectively:
Thermal Expansion Management in CPVC Installation
Proper installation of plumbing systems must account for thermal expansion and contraction, particularly in hot water lines. FlowGuard CPVC plumbing pipes are designed to accommodate a safe degree of movement within water distribution systems, avoiding damage from natural bending in necessary areas. Implementing measures such as expansion loops, offsets, or deflection mechanisms can significantly enhance the durability and performance of the piping system, preventing early failures.
Ensuring Compatibility of Materials with CPVC
FlowGuard CPVC is generally compatible with a broad range of common ancillary materials, making it versatile for integration with other systems like copper or galvanised steel pipes. However, it's crucial to use only specially approved compatible materials, such as cutting oils, thread sealants, and hangers, to avoid chemical incompatibilities that could degrade the CPVC. It is advisable to consult the FBC System Compatible Program whenever integrating FlowGuard CPVC with non-CPVC materials to prevent any CPVC pipe problems related to material incompatibility.
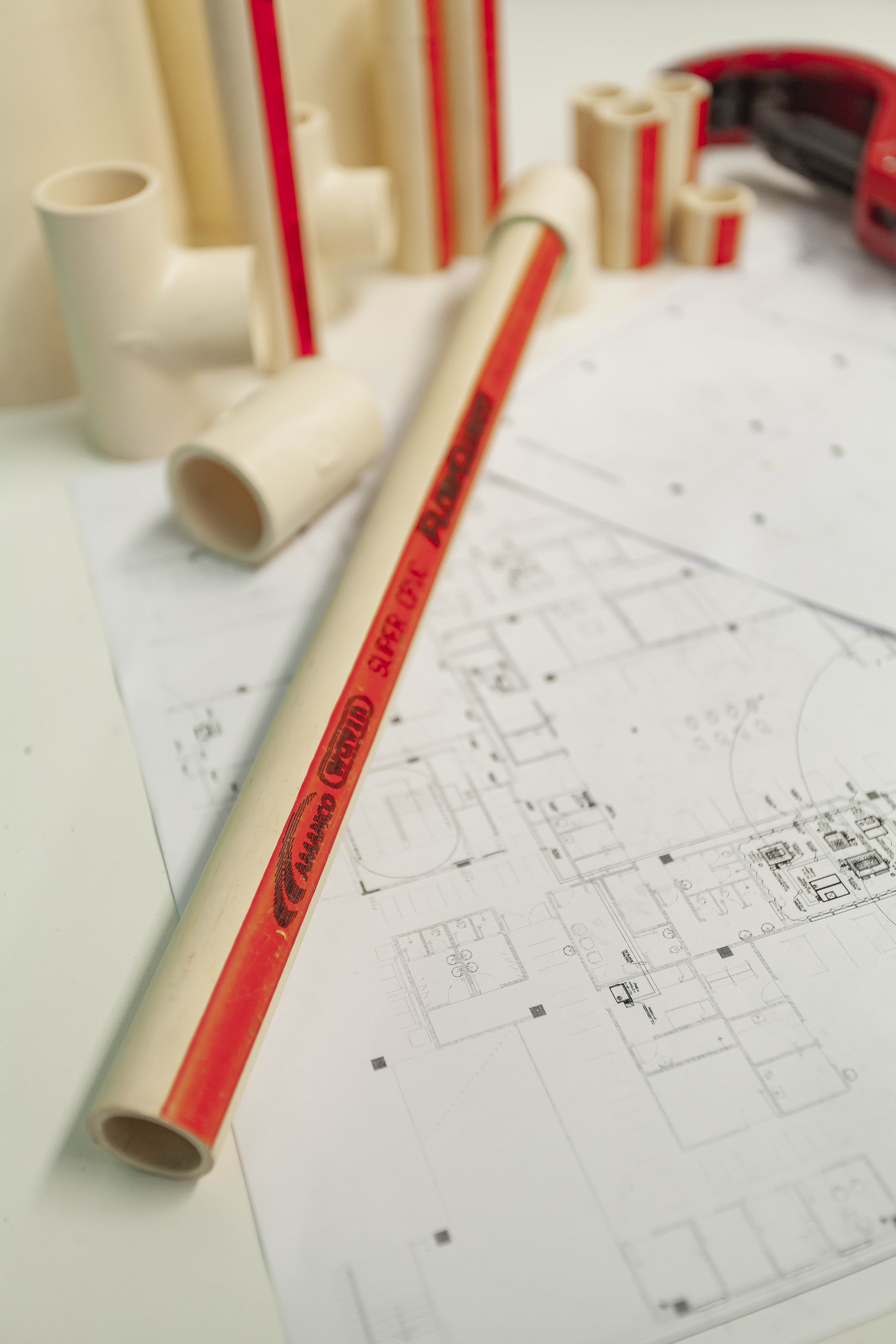
Addressing Cracks and Repairs in CPVC Pipes
Mishandling of CPVC pipe repairs can lead to repeated defects and unnecessary costs. To effectively repair aged or cracked CPVC pipes, it's important to make clean, square cuts to maximise the surface area for a strong solvent cement bond. Ensuring the pipe is free from residual water, sand, or paint is essential to avoid interference with the bonding process. When cutting the pipe to remove a crack, the cut should be made at least 2 inches beyond the crack to ensure a square end for a new fitting.
Handling Solvent Cement Properly During CPVC Installation
CPVC installation challenges can arise from environmental factors, such as high temperatures which can cause solvent cement to dry more quickly. This demands faster preparation to ensure a proper bond is achieved. Solvent joints should always be executed while the cement is wet, and it may be beneficial to perform this in cooler settings to allow more working time. If the solvent cement dries before joining, the pipes and fittings affected must be cut out, discarded, and the process must restart, as dry solvent cannot create a molecular bond.
The Importance of Trained Installers
The benefits of FlowGuard CPVC, renowned for saving time and reducing costs in the plumbing industry, are best realised when installations are performed accurately and thoroughly. To facilitate this, training resources and technical support are continuously available to plumbing professionals. Engaging with these resources helps in avoiding CPVC pipe problems and ensures that every installation upholds safety and performance standards.
To gain deeper insights into the proper installation of FlowGuard CPVC in various settings and how to circumvent common CPVC pipe problems, download the comprehensive "FlowGuard Pipe and Fittings Installation Guide."
DELIVERING
RELIABILITY
For more than 50 years, FlowGuard® Pipe and Fittings has provided reliable hot and cold water plumbing systems to residential and commercial buildings around the world.
DELIVERING
RELIABILITY
For more than 50 years, FlowGuard® Pipe and Fittings has provided reliable hot and cold water plumbing systems to residential and commercial buildings around the world.